【1】簡易型の種類
「簡易型」というのは標準金型を基準として、その構造を省略したり素材を安価で加工しやすいものに変えたりすることでコストを抑えた金型のことです。少量生産を前提とした製造の場合、標準型と比べて制約が生じても初期費用を下げなくてはならないことも多く、ニーズが増大している分野と言えます。
とはいえプラスチック部品を作るための簡易型には、どのようなものがあるのでしょうか?ざっと見てゆくと以下のように大きく7つの分類に分けられると思われます。
素材ごとに大きく「鉄製の簡易型」、「非鉄金属製の簡易型」、「樹脂製の簡易型」に区分することが出来ます。
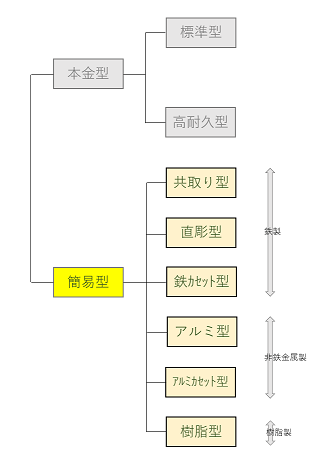
【2】鉄製 簡易金型の特徴
鉄製の簡易型は、使用する素材こそ標準型と同様の「鉄」を用いているものの、その構造をより簡便なものとすることでコストを落としている簡易型のことです。素材に鉄を使用していることから、耐久性は高いものが多く1万~5万ショット程度は製造できる簡易型となります。
特に共取り金型と直彫型については、業者によっては「本型」と主張する方もいらっしゃいます。簡易型の弊害も少ないので、ハードルが低い簡易型と言えます。
共取り型
プラスチック製品は1部品単体で成立することは殆どなく、幾つかの部品を組み合わせて使用します。こうした複数の部品を同じ金型の中に彫り込んでしまうのが「共取り型」という簡易型です。標準型の多数個取りに近い構造になるので、製品の品質も十分担保され易い金型です。「材質が違うので共取り金型にできないのではないか?」と考える方も良く居ますが、ゲート部分を切り替えることで対応は可能です。
ただし多くのスライドや傾斜ピンが必要な部品形状だと、一つの金型に収めることが出来ないのでこうした共取り型にすることが出来ません。また大きさが異なる部品を同じ金型面に彫るために、小さな部品でも大きな機械を使う必要が出ること、部品のサイズ差により金型が歪み耐久性が下がることなども、この共取り型が有する欠点となります。少量生産の産業機器などで用いられることが多い簡易型で、得意とする生産量(生涯)は2千~5万程度です。
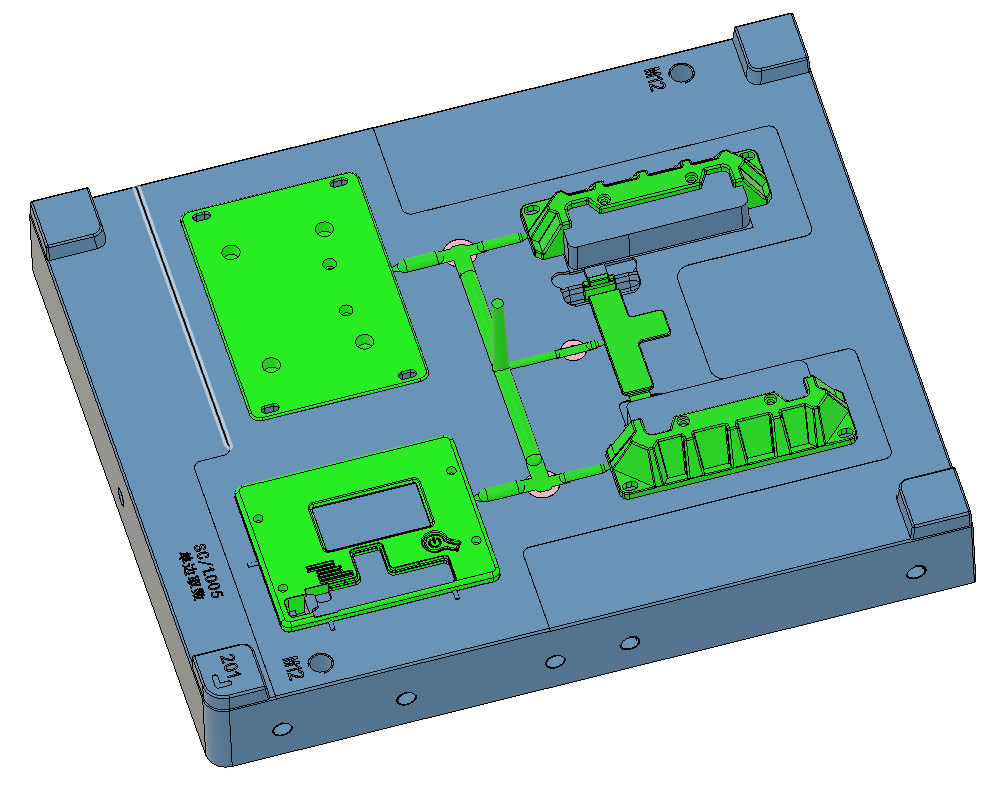
直彫型
標準型ではキャビコアは金型鋼材を使って製作し、その周りを金型躯体(モールドベース)で覆って製造しますが、直彫型では金型鋼材を使わずモールドベースに直接部品形状を彫り込んでしまいます。同じ鉄とは言ってもモールドベースに使われる鉄(S50Cなど)は柔らかく、面もきれいに磨けないので金型に適していないのですが、それでも鉄ですからそれなりの品質で作ることはできます。キャビコアを彫り込まず、金型鋼材を使わないのでその分安価ですが、どうしても耐久性に劣って(1~3万ショット)しまう点が弱点です。おもちゃや雑貨などで用いられることが多い簡易型で、得意とする生産量(生涯)は1千~3万程度です。
鉄カセット型
金型の作り方で分かる通り、金型躯体(モールドベース)は毎回金型ごとに準備されるものです。とはいえ実際に製品製造に一番必要なのはキャビコア部分だけですので、モールドベースは使いまわそうと考えたのがこのカセット型です。
モールドベースが不要なのでコストは下がりますが、共通のモールドベースを使用する関係から金型の自由な設計は制約されてしまいます。特にスライド機構をつけるのは苦手です。また生産の度にカセット部を着脱する必要がありますが、鉄は重いのであまり大きなカセットを使用することが出来ません。こうしたことから歯車や細かい機構部品などで多く使用される簡易型で、得意とする生産量(生涯)は500~1万程度です。
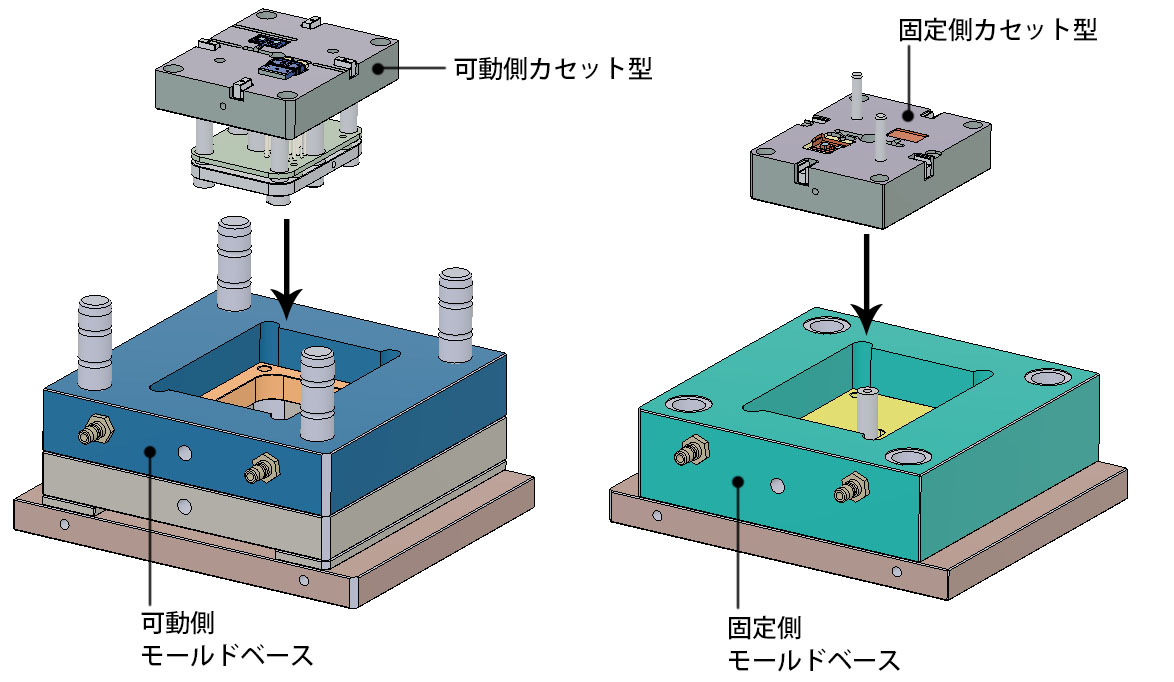
【3】非鉄金属製 簡易金型の特徴
鉄製の簡易型はどうしても重量が重くなり、また加工も本型と同様で結構大変です。そこで軽くて加工性の良い非鉄金属を用いた簡易型も使われています。
アルミ金型
これはキャビコア部分をアルミで製作する金型です。基本は標準型と同じ構造をとっているので外観のきれいな製品が出来ますし、かつ鉄よりも加工時間が短く出来るので短納期の金型製造に向いている方法です。しかしアルミと鉄では余りに強度が異なるので、耐久性は大きく下がります。(せいぜい5,000ショット程度)アルミ価格の高騰と鉄の加工価格の下落によって、コストや納期でのメリットが少なくなり現在では殆ど用いられなくなってきています。
従来は外観が得意な韓国の金型メーカーが、携帯電話の頭出しなどで良く使用していた金型です。
※ZAS型、電鋳型について
アルミ型が流行する前には、亜鉛合金(ZAS)を鋳造して金型を作る「ZAS型」、電気厚メッキで銅で製品形状を作って周りに充填剤を流す「電鋳型」などが、特に深さがあって加工しづらい形状の金型として良く使用されていましたが、工作機械の能力向上と、銅や人件費の高騰によってこうした高い材料を使って手間をかけて作る簡易型は事実上消滅してしまいました。もし古い本に紹介されていても、現代にはないものと解釈した方が良いでしょう。
アルミカセット
アルミ型と鉄カセット型の弱点を補って作られたのがこの「アルミカセット型」です。鉄カセットと同様に共通のモールドベースを使いますが、中のカセット部分をアルミにするので鉄よりも遥かに軽くすることが出来、より大型のカセット(日本国内では400×500ミリ程度の大きさまで)を使うことが出来るのが特徴です。
アルミを使用することで耐久性が劣るため、あくまで少量生産に特化した製造方法です。当社(テクノラボ)及び撤退したプロトラブズ社が採用している方法で、外観部品から機構部品まで幅広く使われています。得意とする生産量(生涯)は50~3千程度です。
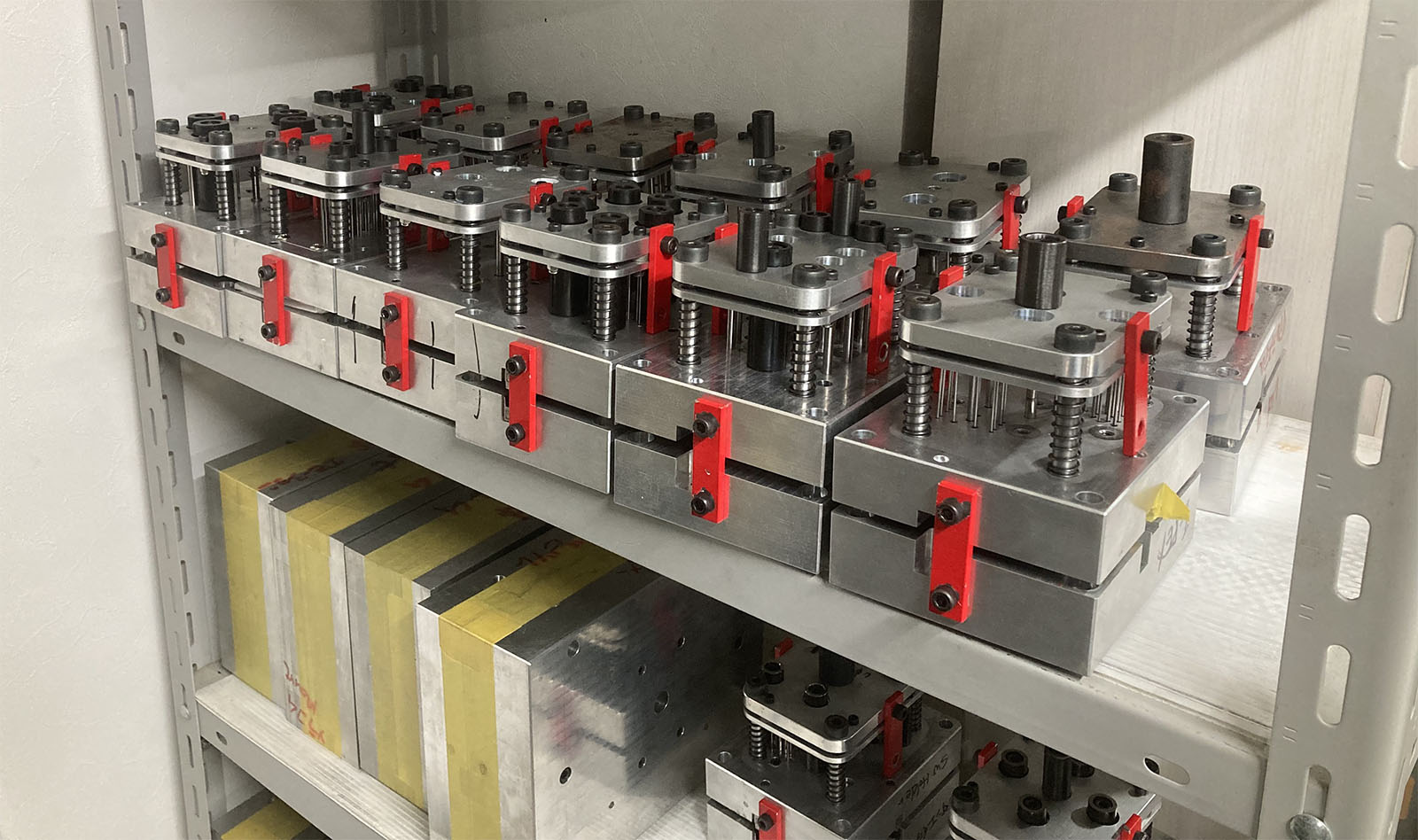
【4】樹脂製 簡易金型の特徴
鉄やアルミでも金型が出来るなら、樹脂でも出来るのでは?と考えて作られているのが樹脂型です。その原点は古く、プラスチック草莽期にエポキシ型を作った時期まで遡りますが、現在残っているのは3Dプリンターを用いた簡易型のみです。
3Dプリンター型(デジモ)
3Dインクジェットプリンターを使って金型を作るのがこの簡易型です。近年の3Dインクジェットプリンターの造形精度は高く、スピードも中々向上しているのでこれを金型として使用するという考えが誕生しました。長野県のスワニー社が行っているデジタルモールド(デジモ)が特に有名です。わずか1~2時間で金型が完成し、トライ成形できるという夢のような技術です。
現在はまだあまり大きなモノがつくれないこと、材料費の関係もあって価格は凄く安いというわけではないことが弱点ではあります。とはいえ今後の技術進展で大化けする可能性もある簡易型技術です。
※METZ型について
3Dプリンター型の少し前まではエポキシにアルミ粉を混ぜたMETZという材料が流通しており、これを流し込んで簡易型を作るMETZ型というものが樹脂型の主流でした。しかし現在ではMETZ材の供給業者もいなくなり、また加工に技能が必要なこともあって消滅してしまいました。残念なことです。
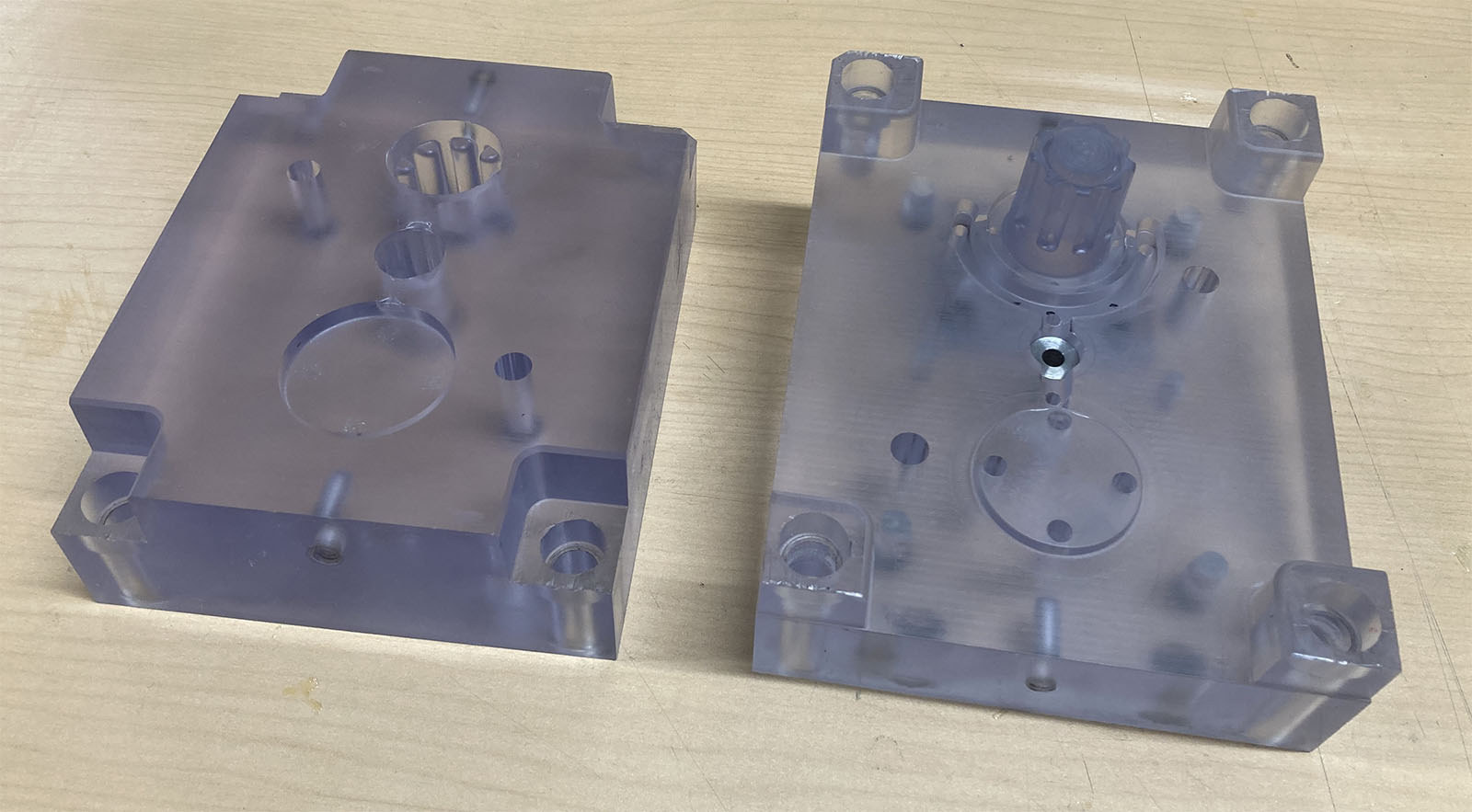
【5】簡易金型で注意すること
以上のように紹介した簡易型ですが、標準型と比較して共通して次のような相違点があることを十分留意して利用を検討すべきでしょう。
1)初期費用を抑えるほど、部品単価は高くなる(逆もまた然り)
当然ですが初期費用を抑えるには何処かを削って作っている訳です。ほとんどの場合、簡易型では標準型と比べて部品の製造単価は高くなる傾向にあります。初期費用を生涯生産数で配分した時、小量しか製造しないのが明確ならば簡易型は有利です。しかし生産量が増えるほど、生涯コストで見た場合に標準金型が有利になってゆくことには注意してください。
2)出来上がり品質に制限がある
これは特に非鉄金属や樹脂型の場合に言えますが、鉄と比較して強い圧力を保つことが出来ないのでどうしても充填不足になり勝ちです。結果として「ヒケ」と呼ばれる現象が起きやすくなり、面のハリが甘くなりがちです。特に厳しい外観部品に使用する場合は注意が必要です。
3)所有権に制限がある
カセット型や樹脂型の場合、共用で使用するモールドベースはメーカーが自前で準備しているものを使うこととなります。このためこうした簡易型では所有権ではなく専用使用権を与えるのが一般的です。
米国企業のプロトラブズ社が撤退した際、このルールを盾にとって金型を返還しない、あるいは事後の製造保証を一切しないというトラブルが発生しました。残った簡易型業者はそれぞれこうした問題に対策しているとは思いますが、所有権に制限がある点は気に留めて置いた方が良いと思われます。
【6】簡易型以外の生産方法
以上、簡易型について大まかな概略を説明しましたが、簡易型以外にも少量で部品を作る方法があるので、幾つかご紹介します。
真空注型
見本の製品を元に、シリコーンゴムで反転型を作り、ここに液状プラスチック(硬質ウレタン)を流し込んで製品のコピーを取る、「真空注型」という手法も特に少量生産では有効です。液状のシリコーンを流し込んで型を作るため、型代が非常に安価なためです。一方で一つずつ手作りとなるので、部品の生産コストは非常に高くなります。また使用できる材料が限られるので、通常の熱可塑性プラスチックのような材料特性は望めません。得意とする生産量(生涯)は5~50程度です。
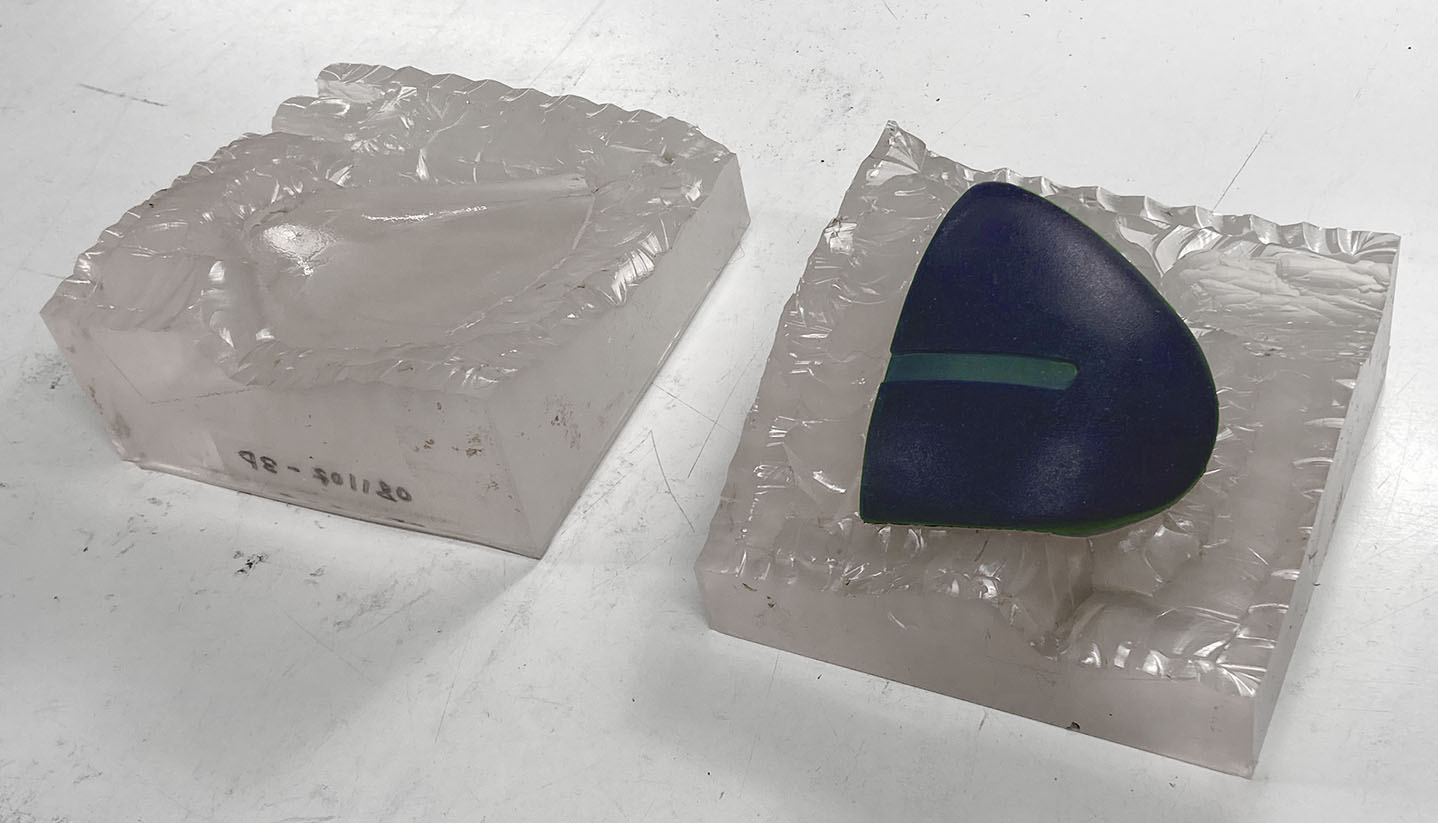
ゴムプレス加工
ゴムを作る方法はコンプレッション成形(熱プレス)と呼ばれ、金型構造が単純で安価な製造方法です。ゴムだけでなく架橋反応する熱硬化性樹脂でも行うことが出来るので、本来少量生産に向いている製造方法です。得意とする生産量(生涯)は5~500程度です。
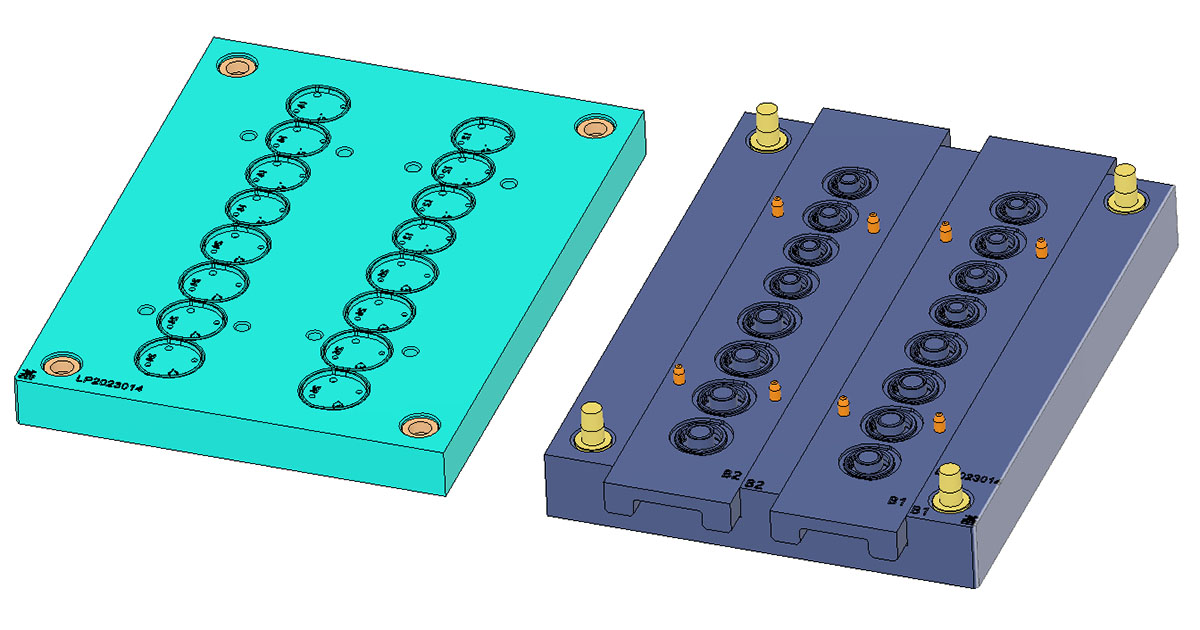
板金加工
プラスチックではなくなりますが、躯体や筐体などを少量で生産する場合、薄い金属の板を曲げて加工する板金加工も考慮に入れる方が良いでしょう。板金加工機は1990年代に大幅に進化したので、少量生産でも金型なしで部品を製造することが出来るからです。一方で金属を使用するので、部品の単価はある程度高くなります。得意とする生産量(生涯)は1~50程度です。
3Dプリンター
2010年代後半に話題となった3Dプリンターですが、今も試作やごく少量の生産では健在です。やはり使用できる材料に限りがあることと、部品単価が高くなることから数量が増えると難しいですが使用場所を考慮すると十分利用することが可能です。外観を問わない内部の構造部材として、特に時間がないときなどに粉体焼結(レーザーシンタリング)タイプの3Dプリンターで作った部品が良く使用されています。得意とする生産量(生涯)は1~50程度です。
旋盤加工(リース加工)
最後にちょっと変わった加工方法ですが、円筒形状で比較的小さなものであれば自動旋盤(リース)を使った加工も有力な候補となり得ます。自動旋盤は金型なしで、かつ比較的量産部品単価も安価になる製造方法です。製造できる形状にかなりの制限があるものの、円筒ものであれば一度は考慮に入れる価値があるでしょう。得意とする生産量(生涯)は5~5000程度です。
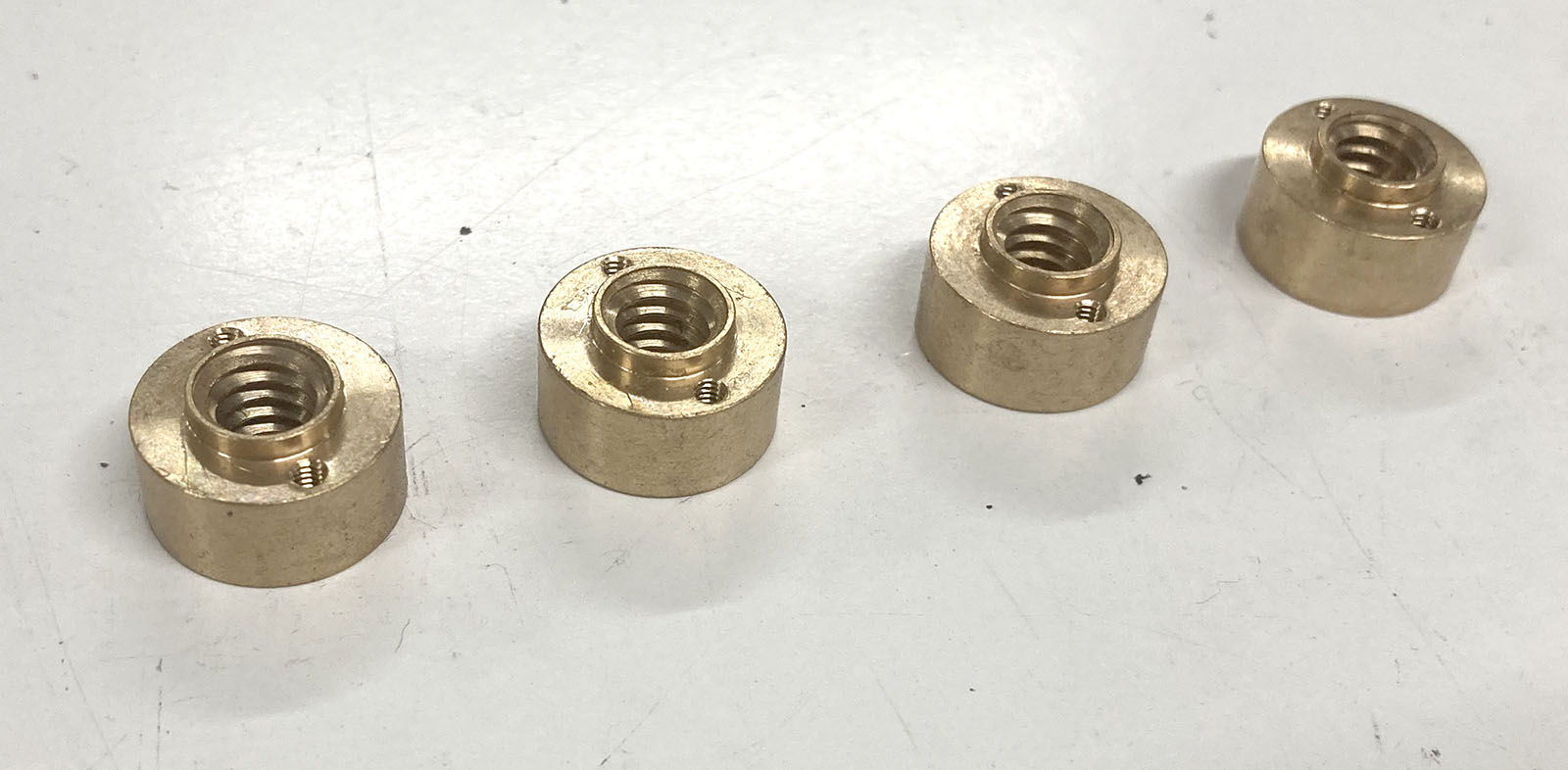